Home » Posts tagged 'awning installation'
Tag Archives: awning installation
Steps in the Roofing Installation Process
Whether it’s asphalt or metal, your roof protects your house from the elements. Getting it replaced is a big job. The first step is prepping the area.
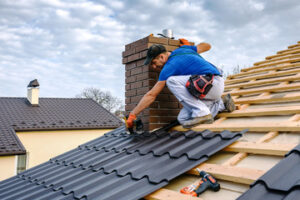
Roofing contractors set up tarps to cover anything on your property that could be damaged by debris falling from the roof. They also cover plants and move vehicles out of the way to ensure everyone’s safety.
Once you’ve decided to re-roof, the contractor will prepare your property for installation by bringing in the necessary equipment. They will lay tarps around the bushes, sculptures, and landscaping features to protect them from falling debris during the roof installation process. They will also park a dumpster in your driveway to make it easy to dispose of any old roofing materials. In addition, they may bring a large magnet to sweep the ground and attic to remove any stray nails from the old roofing material or discarded shingles.
Depending on the scope of your re-roofing project, you may need to move any vehicles or outdoor furniture away from the work area. This allows the crew safe movement throughout your property and ensures their vehicles don’t damage your home or belongings. It’s also a good idea to have your children and pets stay at another location during the roof installation process, as the noise from hammers and nail guns can make them anxious or distract them from their normal activities.
If you have wall-hung pictures or delicate mementos, consider taking them down before the roofing crew arrives. Likewise, it’s a good idea to cover any items stored in the attic as the vibrations from the hammers and nail guns can cause them to shake loose. If possible, you should also consider moving expensive furniture out of the way so it doesn’t get covered in dust or debris.
Once your shingle or metal roof is installed, the final element that is often overlooked is flashing. This is a metal material that is placed around chimneys, windows, joints, and other vulnerable areas to keep water from entering your home. A quality roofer will install the flashing with precision so that it doesn’t leave any leaky spots.
Whether you are having a new asphalt shingle or metal roof installed, it’s important to communicate with your contractor and ask any questions you have. They should be able to explain the installation process in detail, discuss any potential disruptions to your routine, and address any other concerns you have.
Materials
Whether you’re building a new home or replacing an existing roof, the choice of roofing material is critical. It can have a major impact on everything from the exterior appearance to longevity and energy efficiency. Before you choose a material, consider the climate in your area and any special installation or maintenance requirements that may come with it. Ultimately, the right material can add both value and curb appeal to your property while offering superior protection from the elements.
The foundation of any roof is the framing, which consists of rafters or trusses. Rafters are cut on-site from lumber such as 2x10s, while trusses are prefabricated in a factory and craned into place. On top of the framing, a layer of sheathing is installed. This is typically plywood or oriented strand board (OSB), although older houses may have tongue-and-groove sheathing made of sawn lumber.
There are a variety of roofing materials available for your home, from traditional asphalt shingles to clay tiles and slate roofs. The most common roofing material, asphalt shingles, are a cost-effective option that comes in a range of colors and styles to complement any architectural style. These shingles are durable and weather resistant, with a lifespan of 15 to 30 years or more.
Slate, one of the oldest roofing materials, is fireproof and naturally weatherproof, with a lifespan of 50 to 100 years or more for soft slate and up to 200 years for hard slate. They are expensive, however, and require specialized framing during installation to support their weight.
Rolled roofing material is another affordable option that offers fast installation for low-slope roofs, such as those found on sheds and garages. It is available in a wide range of colors and patterns, with a finished look that can be accented by using metal flashing around penetrations and open valleys. Many shingle manufacturers recommend installing an underlayment, usually a #15 asphalt-impregnated builder’s felt or tarpaper. Synthetic underlayments, such as woven polyethylene, are tougher and less likely to tear during installation, and they resist moisture and air infiltration. They also offer additional waterproofing for vulnerable areas such as eaves, valleys and around penetrations.
Installation
After getting the go ahead from you, your roofing contractor will get set up to begin the process. Depending on the size of your roof, this could take a few hours. They will cover sensitive areas of your property with tarps, have a dumpster delivered, and set up wooden boards to cover anything around the base of your home like plants or the air conditioning unit. They will also cover any open drains to keep small pieces of debris from getting in and blocking them.
If you are re-roofing, your roofer will talk with you about the different options for the new roofing materials. You can choose from dimensional shingles for a beautiful look, three-tab shingles to save money, wood shakes for a natural appearance, metal sheeting for easy maintenance, and clay tiles for extreme durability. You can also add new vents for increased attic ventilation to improve energy efficiency.
Final Inspection
The final inspection is the last step in the roofing installation process. It is the last chance for the contractor to make sure everything was done correctly and is code compliant. During this inspection, the inspector will walk the roof, validate the nailing pattern, look at the flashing in the areas needed, and overall ensure the work was complete to minimum code. If re-roofing is being performed, the inspector will also need to walk the deck and verify that the proper underlayment and/or roof cover was applied and that all areas were covered. Affidavits will be required for re-roofing projects, as the inspector will need to see evidence that the project was completed with correct materials.
The inspection requirements will vary, but the best way to prepare for a final inspection is to have extensive documentation of the project. This includes the obvious, like building plans and proof of passing previous inspections, but it should also include photo records of any changes or revisions made throughout the construction phase. Having this documentation can help the inspector understand the reasoning behind any decisions or issues that may arise. It can also save a lot of time and frustration during the inspection if it is clear that the contractor has the documents to back up their actions.
Many inspectors will provide a checklist prior to the inspection to give contractors an idea of the key items that they should focus on. This can be helpful, but it is important to remember that the key issues will depend on the specifics of the job. For example, minor issues that do not pose a safety risk may be able to be addressed with a quick change or revision, while serious problems will need to be corrected and resubmitted for approval.
It is vital to hire a professional roofer to inspect your new roof and to ensure that it was installed properly. The inspection will uncover any small mistakes that could become big, expensive problems down the road. Skipping the final inspection can also lead to a delay in getting things up to code and obtaining the necessary permit, which can result in costly fines down the line.